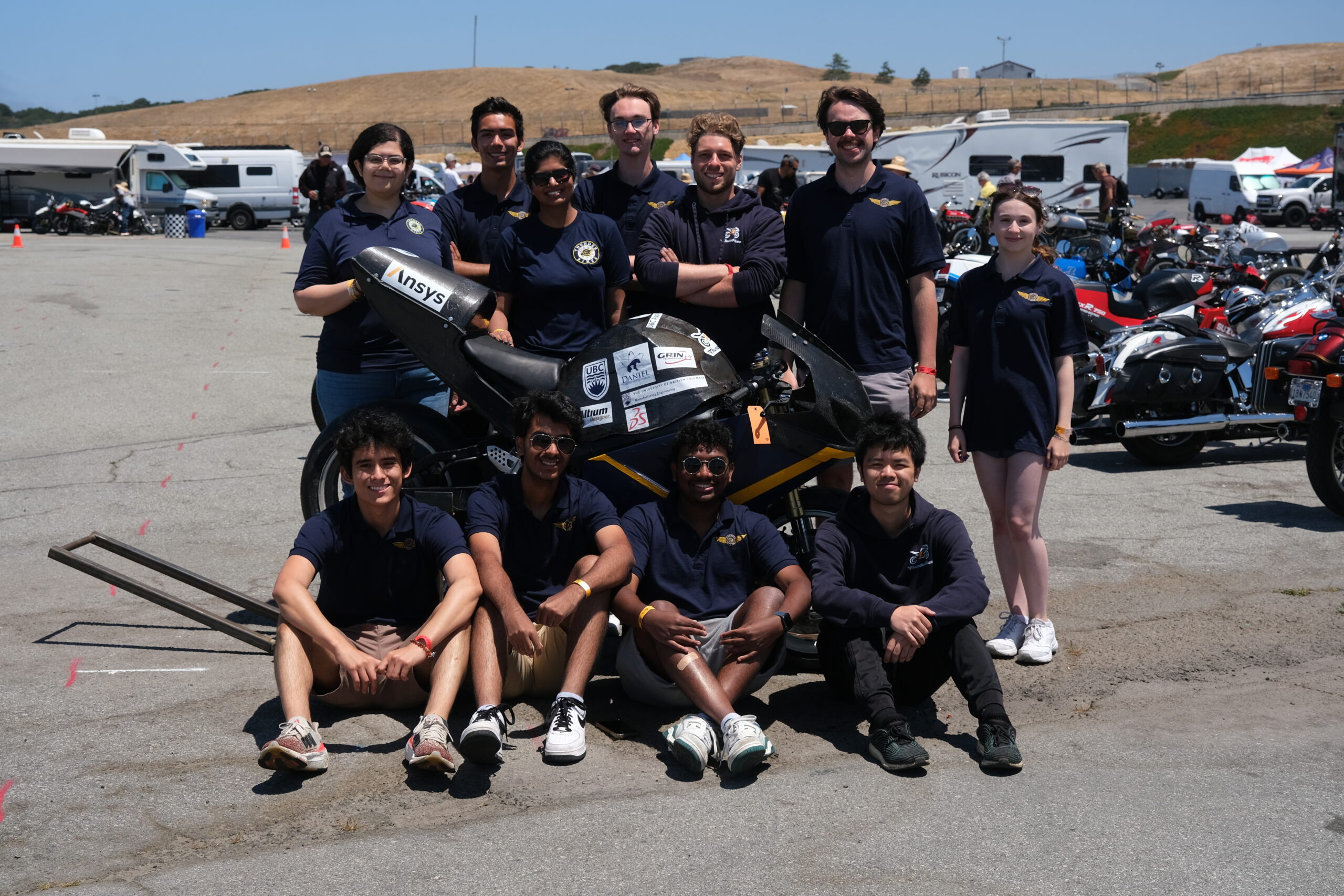
Engineering the Future of Electric Racing
The UBC ThunderBikes team competes in the renowned AHRMA Classic MotoFest at Laguna Seca, a premier event for electric motorcycle racing enthusiasts. Hosted by the American Historic Racing Motorcycle Association (AHRMA) at the legendary WeatherTech Raceway Laguna Seca in Monterey, California, this competition brings together a diverse field of electric and traditional motorcycles.
Our team participates in electric racing classes, where we push the boundaries of sustainable performance alongside industry leaders and other innovative engineering teams. This competition challenges us to showcase our engineering expertise and test our electric racing motorcycle against industry standards. At the heart of our participation is a commitment to advancing electric vehicle technology, building a bike that is not only fast but also represents the future of motorsports.
Mechanical Team
The mechanical team of ThunderBikes is responsible for everything that’s… well… mechanical. This includes the structural components of the bike, such as the battery casings and lower frame. They also build the bike’s cooling system and design the mounting fixtures for the motor and high-voltage electronics.
Battery – Mechanical Team
The mechanical battery team is responsible for all structural aspects of our batteries. This includes creating metal battery frames and mounting the batteries to the bike frame. The mechanical battery team works closely with the electrical battery team on tasks such as battery layout, busbar design, and routing wires and fuses.
Cooling Team
The cooling team is responsible for designing and implementing the bike’s heat management system. This involves performing calculations to determine the heat generated by the bike and evaluating the performance of the cooling system. Additionally, wind tunnel testing has been conducted to assess the effectiveness of different radiator placements. The cooling team designs and manufactures the liquid cooling system, including in-house battery cooling plates.
Frame Team
The frame team develops the bike’s lower subframe. This tubular steel subframe includes mounting points for the batteries and motor, serving as a critical structural component of the bike. The frame team is also creating a CAD model of the entire bike in SolidWorks.
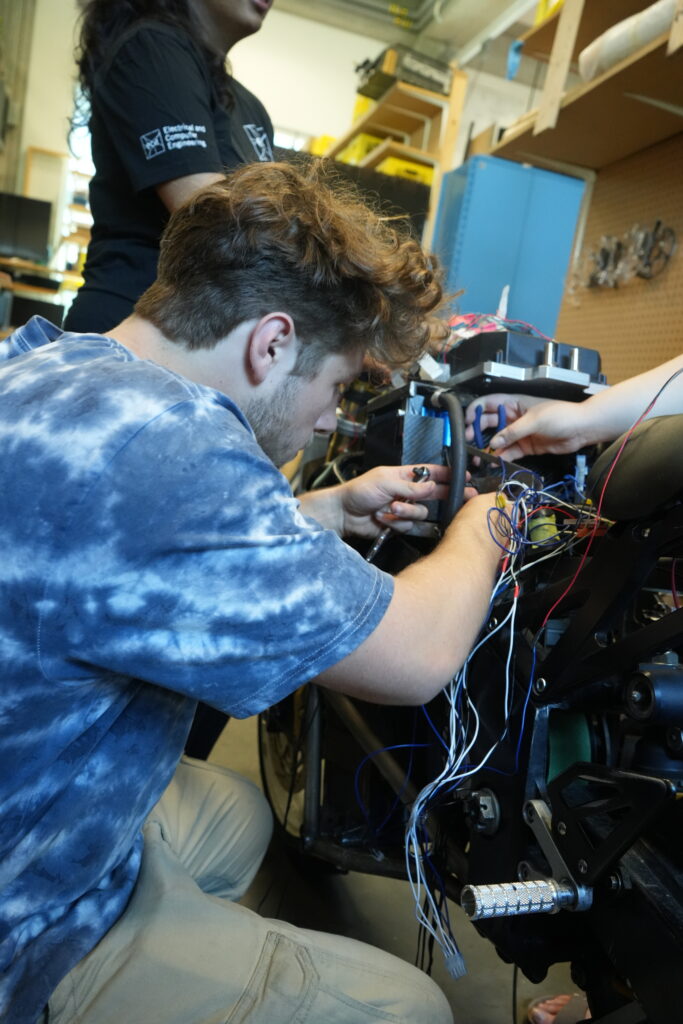
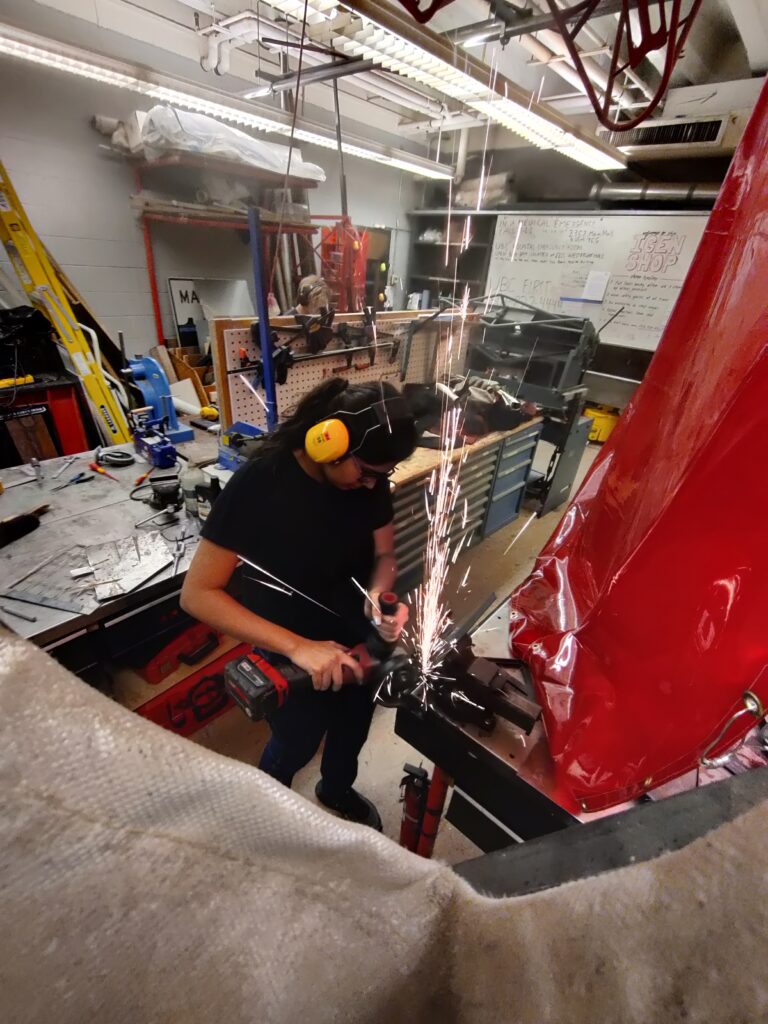
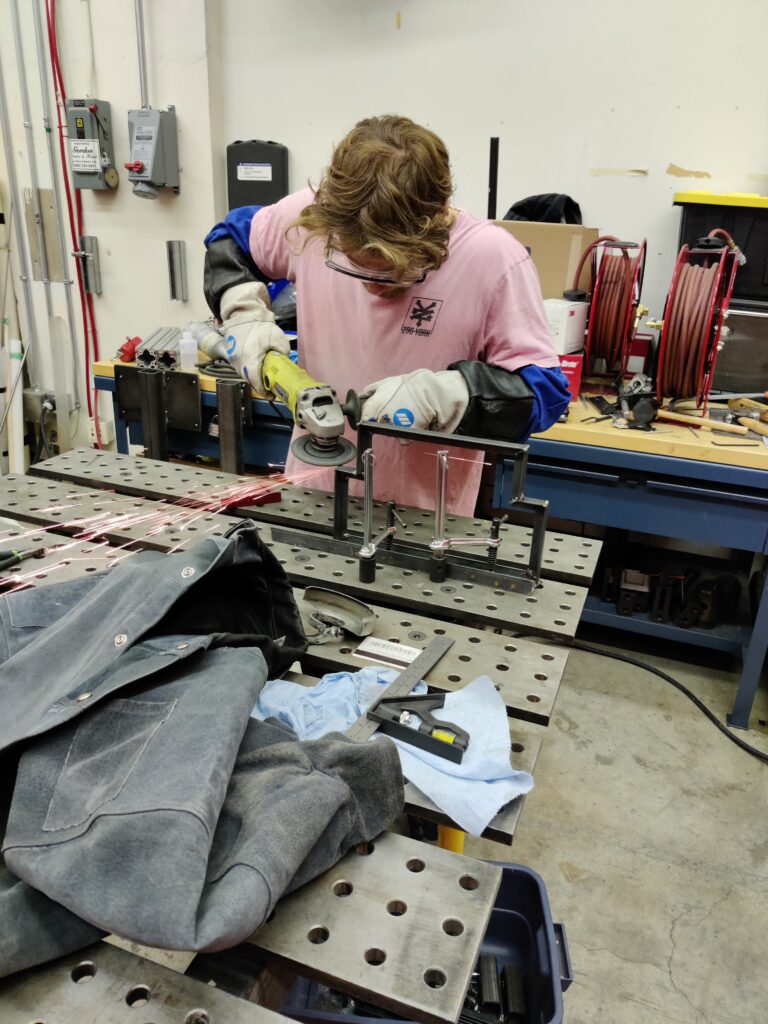
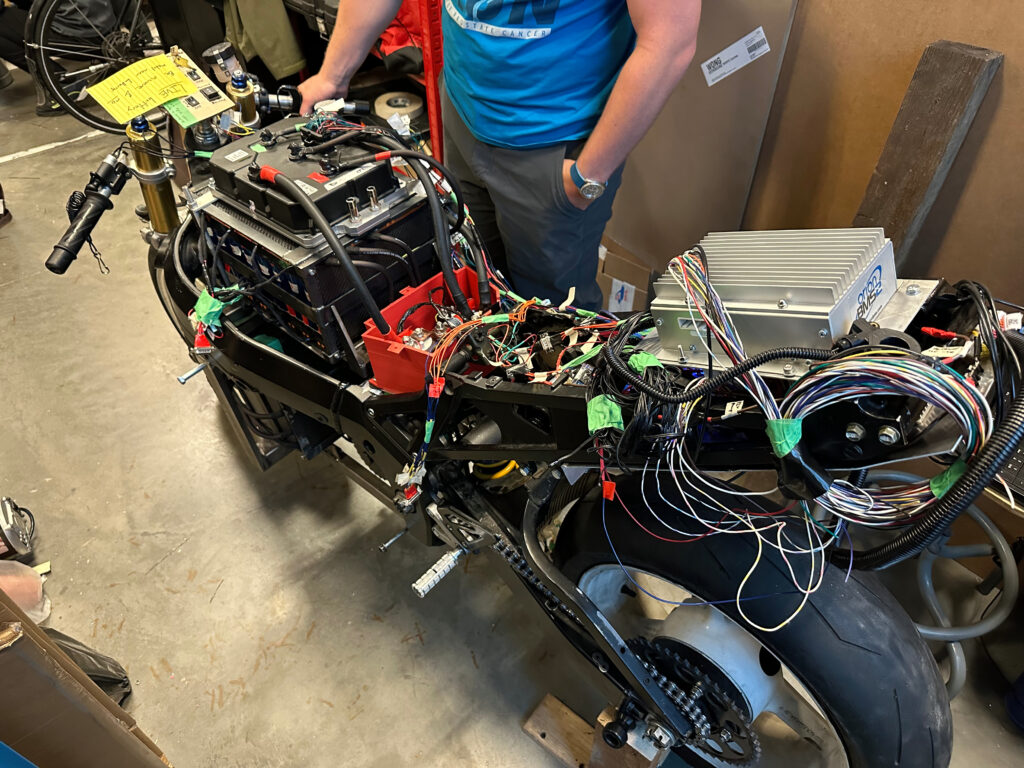
Electrical Team
Battery Team
The underlying system for the team. The electrical battery team works closely with the mechanical battery team and control circuitry team to ensure a high performance LiPo battery pack assembled in house can be safely used to power the bike. Their work also includes working with the battery management system to ensure no faults and to maximize performance.
Control Circuitry Team
Being the brains of the bike, this team has to ensure that all logic runs properly. If an electrical signal needs to stop power to the bike, this team will do it. From relays to logic gates, they implement critical systems to ensure the bike behaves as expected. This team collaborates with all other electrical subteams to ensure each system can be interconnected.
Dashboard Team
One of the most important features to the rider of the bike. The dashboard team works to ensure all valuable information that a driver would need is being displayed on an intuitive and sleek UI. They have to work closely with the firmware team to ensure data transmission between the bikes components and the dashboard is reliable.
Firmware Team
Electrical signals need to be processed and that’s what firmware does. This team focuses on systems which cannot be solved by the control circuitry team and instead implement software to do so. This team helps process communication signals to ensure that all electrical components can work with each other, regardless of communication protocol.
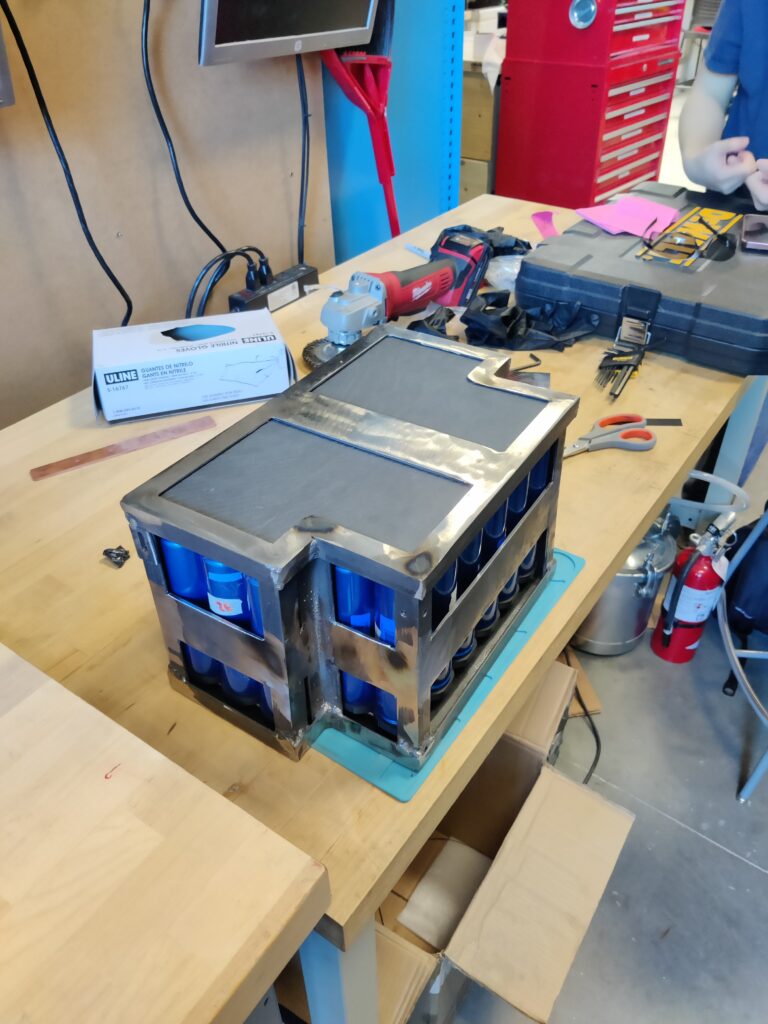
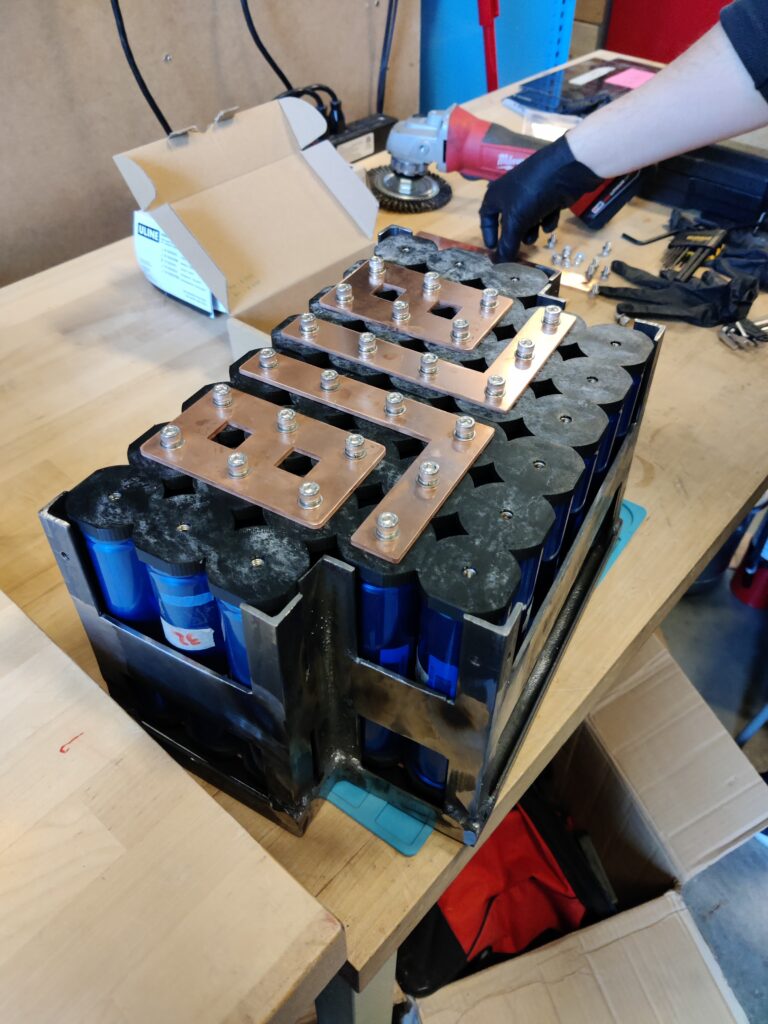
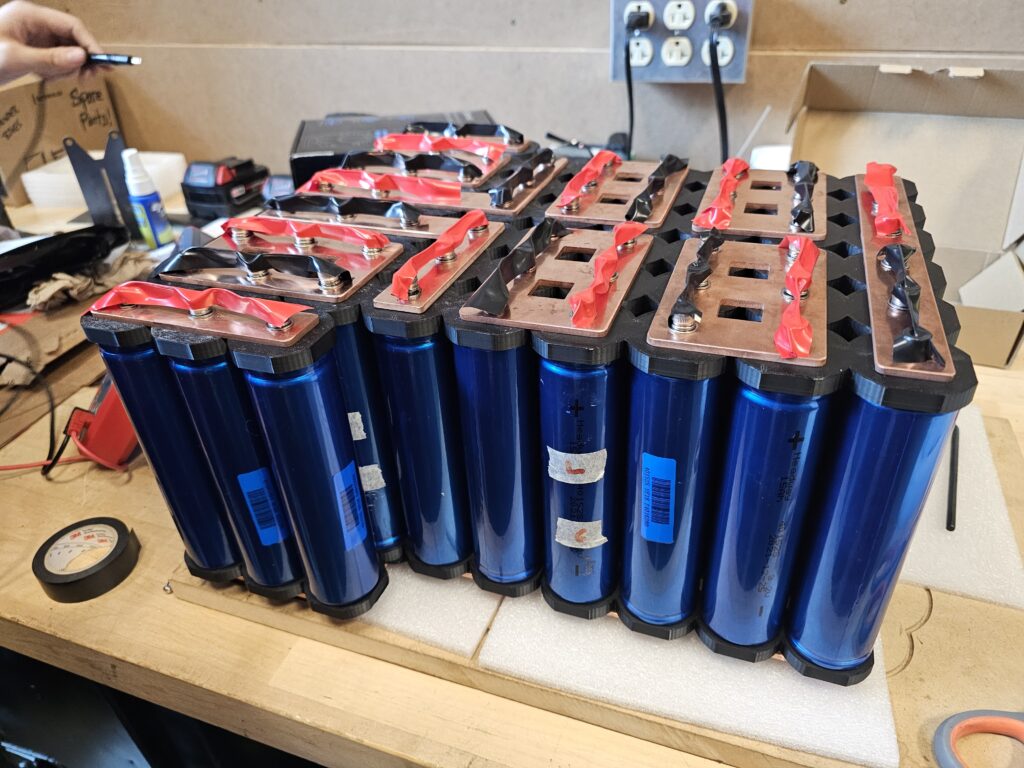
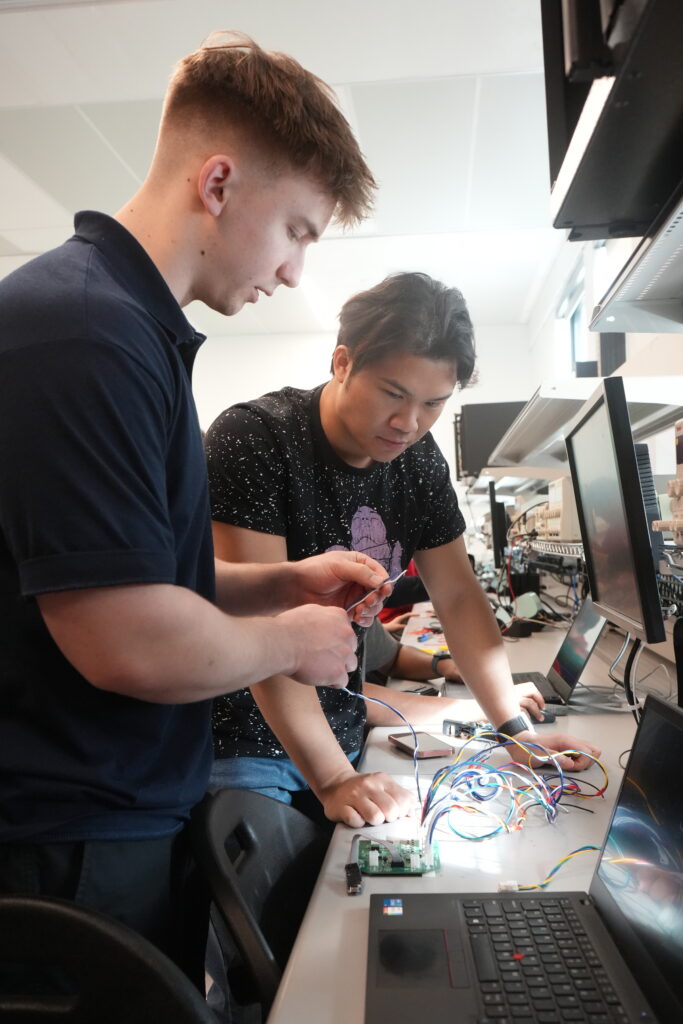
Aerodynamics Team
The Aerodynamics and Composites team is responsible for the design, optimization, and fabrication of the external body and aerodynamic components of the electric motorcycle. The team focuses on enhancing the bike’s aerodynamic performance, structural efficiency, and system protection. This involves iterative design processes and computational simulations to fine-tune the fairings’ geometry.
Composite Structure Development
We are designing and fabricating composite structures to achieve a balance between minimal weight and maximum strength. Advanced materials and techniques, such as carbon fiber layering and resin infusion, are used to ensure the bike meets the rigorous demands of high-performance racing while remaining lightweight for optimal handling and efficiency.
System Protection
Another focus area is the development of protective components for the bike’s body to safeguard critical systems, including the battery, motor, and electronic controls. These components are designed to withstand impacts and environmental challenges, ensuring durability and safety under both competitive and real-world conditions.
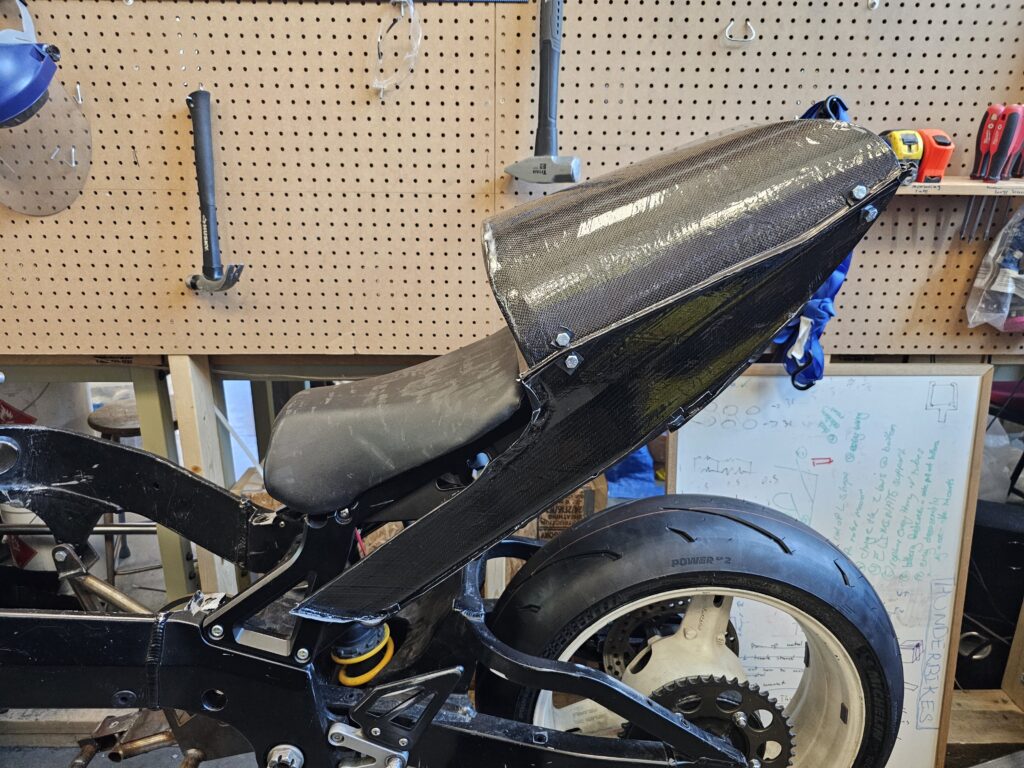
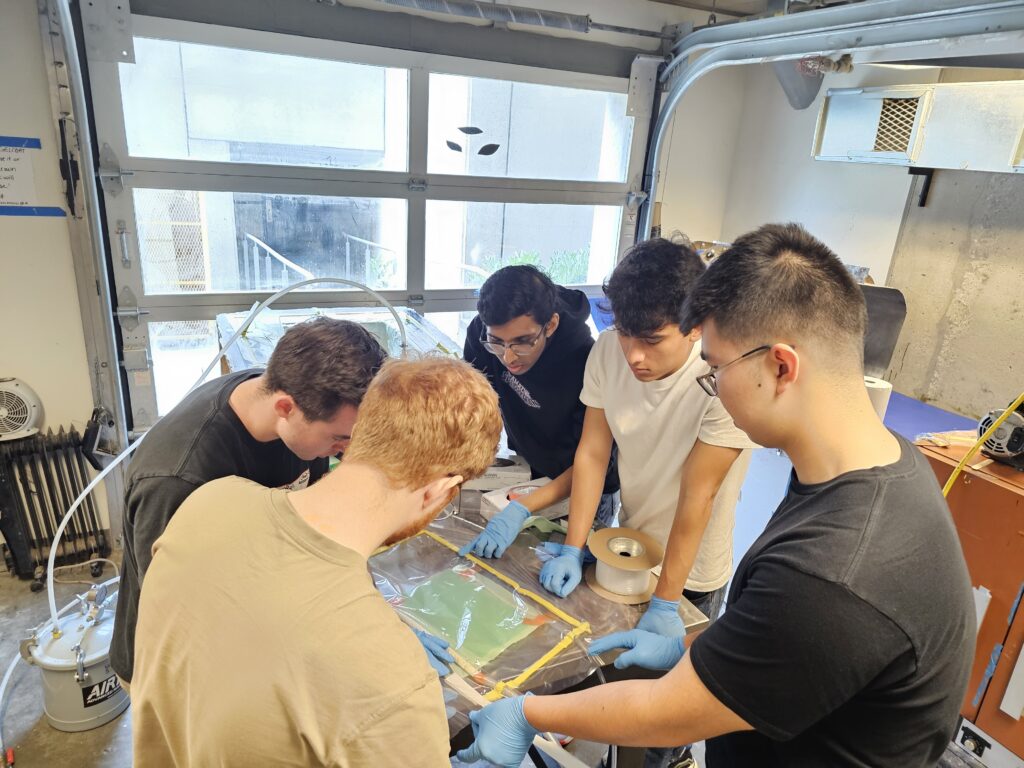
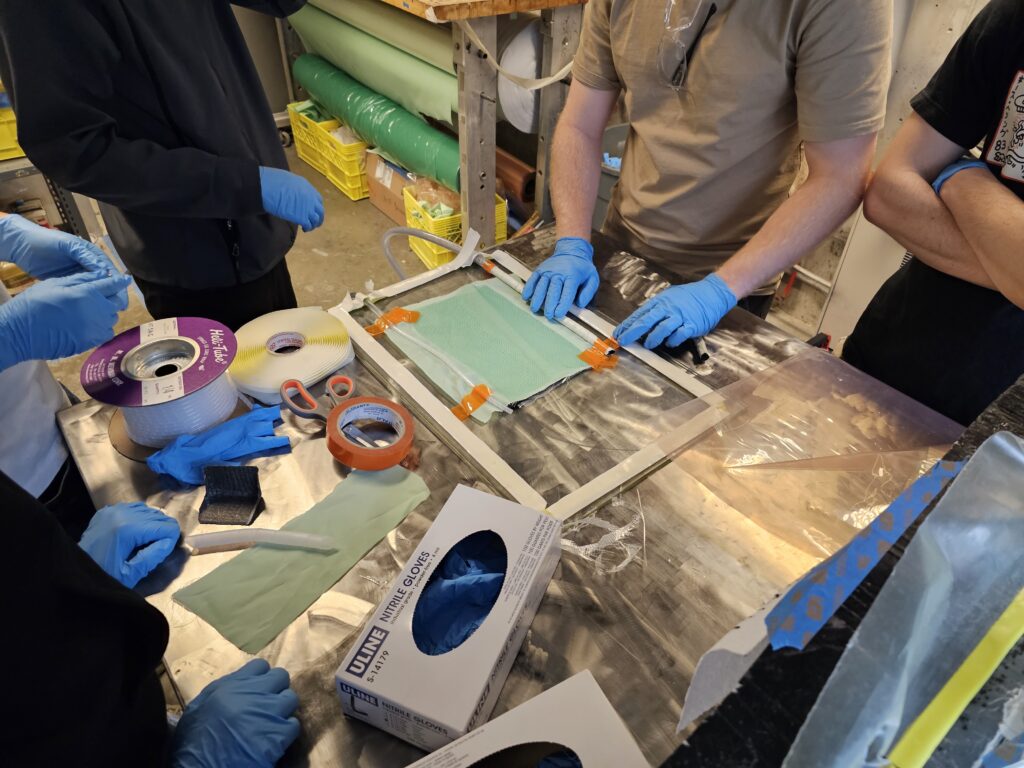
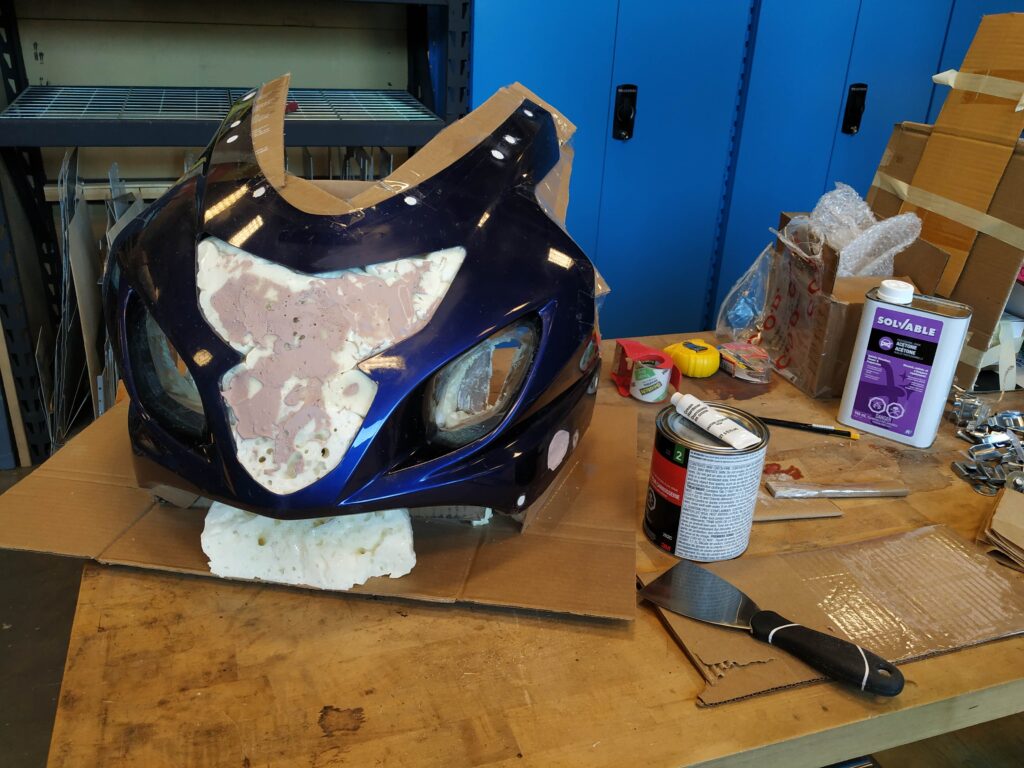
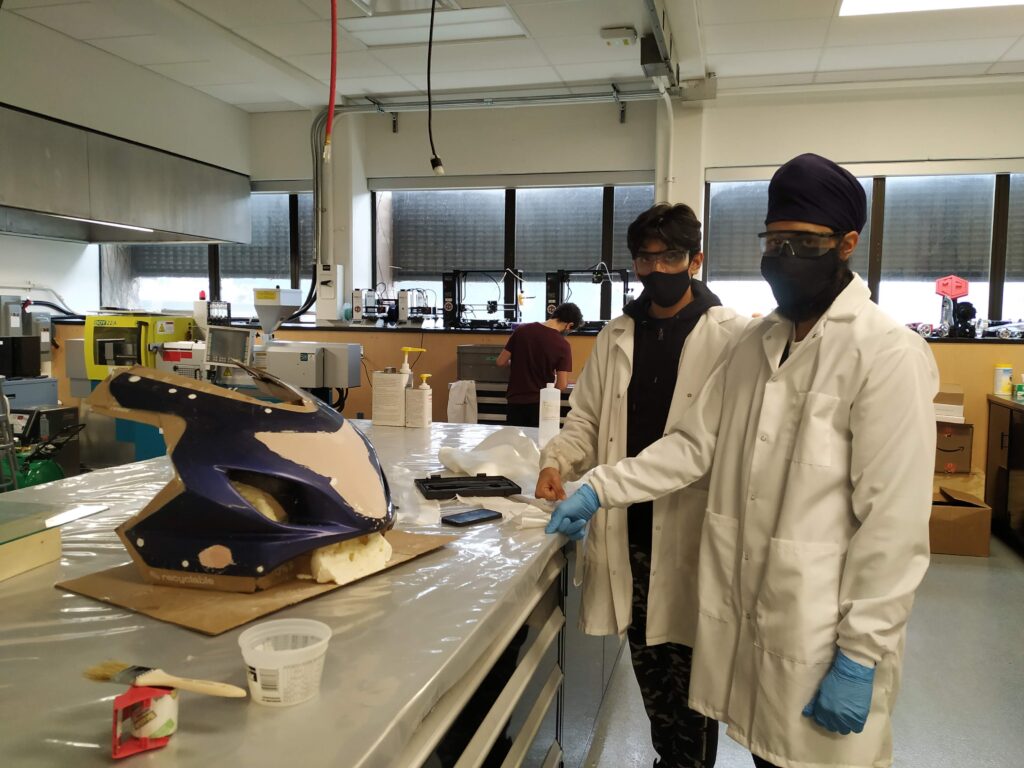